In the U.S., we experience 3.1 nonfatal injuries and illnesses for every 100 workers. Of course, some occupations are riskier than others, and every industry has different averages. Some of the workplaces with the highest incident rates include non-veterinary pet care services and nursing and residential care facilities, each with over 11 incidents per 100 workers. Every workplace has unique safety concerns. An office might have higher rates of obesity and injuries such as carpal tunnel syndrome. Meanwhile, a factory or warehouse will have more risks associated with heavy equipment.
What are the leading causes of work injuries? Across the board, overexertion, falls, contact with objects and roadway incidents top the list. Luckily, you can minimize risks and prevent the majority of accidents by following some simple safety tips.
1. Set Safety Protocols
First, identify the potential risk areas throughout your workplace. Different companies and individual job roles can have various hazards associated with them. For each hazard, draw up a safety plan designed to prevent injury and cut out potential threats. The Occupational Safety and Health Administration (OSHA) creates safety standards for many accident-prone industries. If you’re not sure which safety protocols you need to use, the OSHA guidelines can get you started.
What are the most common workplace accidents? While accidents can vary by the line of work, several injuries are most common:
- Overexertion: Heavy lifting and repetitive motions lead to 33.54% of lost-workday injuries. If this is a risk factor in your workplace, focus on proper lifting techniques and encourage frequent short breaks.
- Contact with objects or equipment: Impacts with objects, collapsing structures or getting caught in machinery accounts for 26% of workplace injuries. A workplace with mechanical equipment or tall structures should develop corresponding protocols. Store heavy objects close to the floor. Be sure employees stay aware of moving machinery and wear personal protective equipment (PPE).
- Slips, trips and falls: Falls of any kind lead to 25.8% of injuries resulting in lost workdays. Keeping floors clear and placing ladders on even surfaces are critical safety protocols.
2. Create Emergency Procedures
Besides day-to-day safety rules, employees and leaders should know what to do when accidents occur. When emergency procedures are clearly defined, people can spring into action when needed. These valuable seconds can make injuries less severe and get people the help they need. According to OSHA, an emergency action plan should have the following basic information at minimum:
- A best practice for reporting fires and emergencies.
- An evacuation policy and procedure.
- Emergency escape procedures, which include route assignments, floor plans, maps and areas to retreat to.
- Names, titles and contact information of internal personnel and first responders to contact during an emergency.
- Procedures for employees to perform or shut down critical operations, use fire extinguishers and perform any vital risk mitigation before evacuating.
- Medical and rescue duties for designated workers.
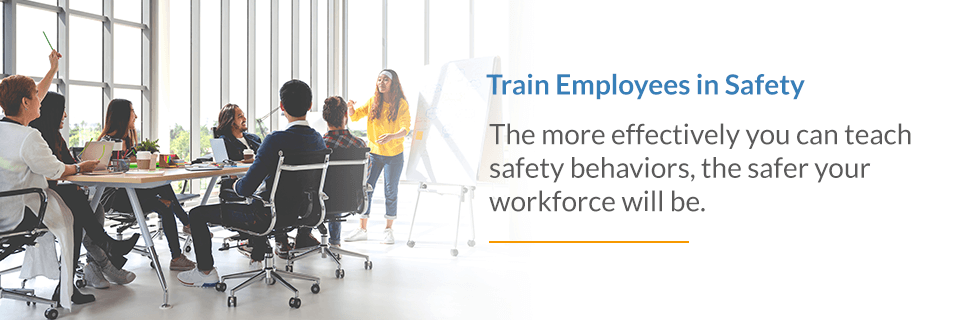
3. Train Employees in Safety
Communicate safety protocols and emergency procedures to all employees. Educate all employees on common workplace accidents and how to avoid them. New employees should learn how to stay safe while performing each of their duties before beginning any work. It’s also vital to teach ongoing safety training courses. Everyone at your company can use a refresher once in a while. The more effectively you can teach safety behaviors, the safer your workforce will be.
4. Give Employees Safety Equipment
The necessary PPE you need to provide varies by industry. Healthcare professionals need masks, gloves and other protective barriers. Industrial workwear should be fire-resistant and durable. Food processing workers need antibacterial garments to prevent the spread of diseases. Construction workers need hard hats, reflective vests and protective ear and eye equipment. Look at OSHA guidelines or industry associations for more guidance on the PPE necessary in your industry.
5. Require Proper Footwear
There are many places in the workplace where open-toed shoes can cause injuries. Any area with chemicals, sharp objects or moving machinery should have a strict “no open-toed shoes” policy. Elevated heights, outdoor spaces and wet areas need footwear designed for increased traction.
6. Inform Employees About Hazards and Safety Concerns
There are many ways to keep employees informed about safety hazards. Make workers aware of safety concerns and dangers so they can be more careful.
- Temporary signs for spills: Whenever a spill occurs, put up temporary caution signs to avoid falls. These signs inform workers to tread lightly.
- Signs for permanent hazards: Sharp objects, electrical equipment, stored chemicals and hazardous waste disposal areas should all be visibly marked. High-contrast signs that outline safety procedures can remind people to use caution.
- Daily discussions: An open forum is critical to creating a safety-first workplace culture. A daily huddle is a great opportunity to discuss recent near-injury misses as well as newly-identified hazards and procedures.
7. Maintain Tools and Equipment
Dull knives cause more injuries than sharp ones. Nearly all companies use sharp blades from time to time, be they kitchen knives, farm equipment or box cutters. A dull blade needs more pressure to slice and takes more repetitive movement than a sharp knife. Proper equipment maintenance — of blades and other tools — prevents malfunctions, which could cause injury.
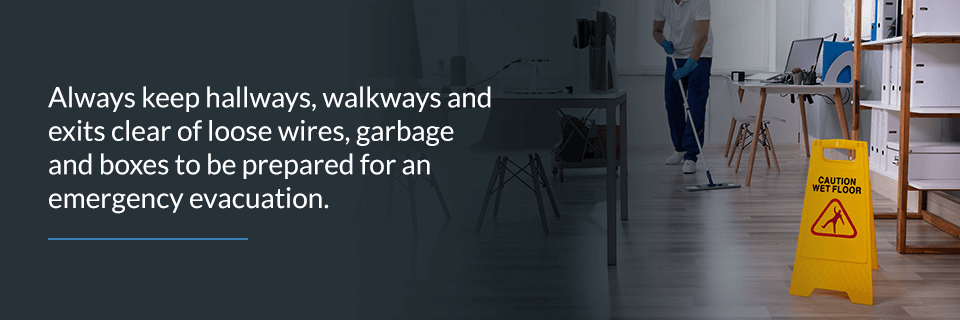
8. Keep Your Workplace Clean
Good housekeeping creates fewer tripping hazards, kills infectious microbes and reduces clutter. Always keep hallways, walkways and exits clear of loose wires, garbage and boxes to be prepared for an emergency evacuation. Unevenly stacked boxes or overstocked shelves can cause a dangerous collapse. Remember to disinfect frequently-touched surfaces regularly, especially during cold and flu season.
9. Invest in Ergonomic Furniture and Equipment
Less-often thought about injuries occur slowly over time. Carpal tunnel, vision problems and back or neck pain can lessen productivity. They can even lead to missed workdays or workers’ compensation claims. A sedentary lifestyle and uncomfortable furniture can lead to aches, stiffness or nerve damage. These injuries, which creep up over time, can even require surgery. You can avoid these types of injuries with ergonomic furniture and tools designed for comfort.
To avoid headaches and eye strain, use screens with adjustable brightness settings. Teach employees about proper posture to help ease back pain. Use a wellness program to encourage physical activity and a healthy diet.
10. Integrate Safety Into Company Culture
You can increase employee satisfaction and reduce injuries using workplace culture. Safety and risk avoidance increase when leadership upholds safety from the top down. When managers model safety procedures in their daily work, other employees are more likely to follow suit in company safety policies. It’s also a great forum for employees to call out unsafe practices or potential hazards. They can give suggestions to upper management without including a name.
11. Conduct Safety Surveys
Anonymous surveys are an excellent way to get feedback on safety. You can find out if employees are familiar with and following company safety policies. It’s also a great forum for employees to call out unsafe practices or potential hazards. They can give suggestions to upper management without including a name.
12. Reduce Workplace Stress
No matter the industry or role, stress causes a slew of safety hazards. Long hours, a heavy workload and conflicts are all common sources of stress. It can lead to difficulty sleeping, depression and issues with concentration. When staying alert on the job is a must, take every effort to reduce workplace stress. Taking regular breaks allows workers to reset and refocus. Forgiving schedules, conflict resolution strategies and manageable workloads can decrease stress and accidents.